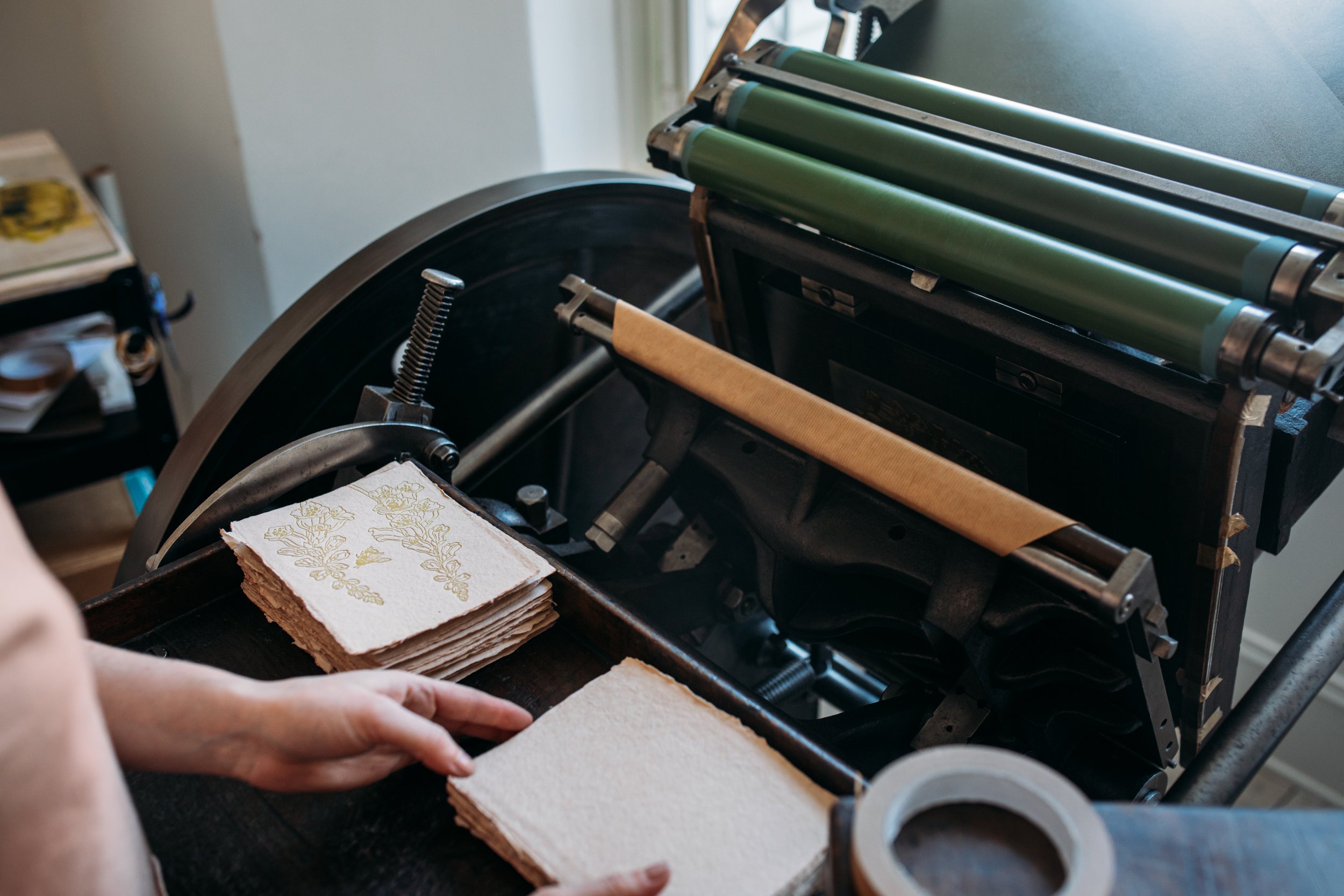
Letterpress printing service
Letterpress is a printing process steeped in tradition and history. There’s nothing quite like that deep fossil-like impression on fluffy, deckle-edged handmade paper and that’s why I believe they are a match made in heaven. The end product is gorgeously tactile – almost pillow-like in appearance – and is able to elevate even the simplest of designs.
Sound like an impression you can’t wait to get your hands on? Take a look below to find out how to place an order, as well as the finer details of this traditional printing process.
(Please note that this printing service is offered alongside my handmade paper service and you will need to place an order for a made-to-order batch of paper in order to use the printing service.)
PLACING AN ORDER
In a nutshell
ONE
Fill in the online order form
This will provide me with all the information I need to send you an invoice direct to your email inbox.
You can also request a quote using this form.
(Heads up - production lead times can vary. Check out the website banner at the top of the page for current lead times.)
TWO
Pay the invoice
After receiving the invoice you have 48 hours to make payment. Payment is required in order to reserve a space in the batch production schedule. Please only place an order when you are ready to pay the invoice.
Payment is via bank transfer or Stripe, a reliable and trusted payment platform.
THREE
Supply your artwork for print
Please check the ‘Guidance for supplying artwork’ section below as I cannot print your designs if you are unable to provide artwork with the correct formatting.
FOUR
Open your parcel!
Once your order is complete and on its way to you in the post, I will email you with tracking information.
After waiting eagerly for the post to arrive, grab a brew and take a moment for yourself while you unwrap your parcel and admire all the lovely, tactile, printed paper goodness!
The finer details
-
Letterpress is a type of relief print where traditionally wooden or metal type and carved blocks were used along with a printing press to create a repeated printed impression. These days the use of polymer plates allows for more innovation in design, however, many of the presses themselves remain in their original condition and the technique remains largely unchanged.
My press is a beautiful Arab Crown Folio manufactured in 1898 by Josiah Wade in Halifax and restored in January 2020 by The Logan Press. Fondly named Arabella, she is a treadle-operated Clamshell platen press.
-
Much of the cost of letterpress is in the production of the printing plates and the set up of the print. Below are the steps required to set up and print a single colour image.
1. Ink is mixed by hand.
2. The ink is transferred to the press and using a treadle mechanised action the ink is spread evenly across the inking disk and the rollers.
3. The plate is attached to the press and test prints are done whilst manually adjusting position and pressure in order to find the perfect alignment and impression on the paper.
4. Using the mechanised action of the treadle causes the rollers to pass over the inking disk and then the plate. A sheet of paper is placed on the press and the mechanised action brings the sheet into contact with the inked plate. Each sheet to be printed is passed through the press in this rhythmic way.
5. Lastly, the ink is manually cleaned off the plate, rollers and inking disk.
Letterpress only allows for the printing of one colour at a time with each colour requiring its own separate plate and all the steps listed above. You can also only print one side at a time and each side also requires its own separate plate and all the above steps. This is worth bearing in mind as multiple colours and double sided printing can significantly increase the cost. It is also the reason why letterpress is more cost affective with larger print runs and not ideally suited to one off single or very small print runs.
-
Unlike many other printers (and with some exceptions), I print exclusively on my own handmade paper. As both the papermaker and the printer, I have been able to develop a deep understanding of how best to work with this unique surface. There is also the added benefit of reducing the travel mileage of the paper when it happens to be made and printed in the same studio.
Because of the natural and perfectly imperfect characteristics of handmade paper, there are a number of things that need consideration. Due to the fluffy deckled edges, it is impossible to achieve perfect alignment. This needs bearing in mind when creating designs. For example, with multiple colours it’s unlikely that the two plates will line up perfectly – I recommend creating designs that don't need the colours in perfect alignment. It is also worth bearing in mind that designs which include borders that are close to the edges of the paper may appear more obviously off centre than designs with more space around the edges. I am happy to look over any designs and provide guidance if needed.
-
1. Artwork must be supplied as a vector. (Artwork created in Photoshop or Canva will not be suitable as you cannot create vectors using this software)
2. Make sure your document is in CMYK mode. All artwork should be in CMYK Black, CMY=0 and K=100%.
3. Recommended minimum line width is 0.35pt, also applies to the finer areas of type (watch those serif fonts!).
4. For dots, a 1.25pt diameter is recommended.
5. Outline all fonts – I may not have your fonts on my system so you will have to convert them to paths/vectors to retain their style.
6. If your design includes multiple colours, you will need to provide each colour as separate files - each will be made into its own plate.
7. For each plate design, make sure every element of the design is grouped together within the file – sometimes the platemakers need to move the design around when preparing the files.
8. Artwork must be supplied as a PDF; one for each plate and in the correct size.
-
I am happy to check over your designs and offer guidance before sending them to the platemakers. I also offer a basic design service with an additional fee for anyone who needs some extra help preparing their artwork for plate making.
You will need to be able to supply the file as a vector in order for me to be able to edit your artwork. I would also recommend outlining any fonts as well as I may not have the same fonts on my software. In some cases (and depending on the style of artwork) it may be possible for me to vectorize it for you.
Please be aware that I am not offering a fully comprehensive design service. If you are unable to provide artwork in the correct file format or if much of the guidance above seems like another language, then I recommend you hire a designer to create your artwork and supply the files.
-
Orders can be placed by using the ‘place order’ submission form.
When I have received your order submission form I will email you an invoice and payment is via bank transfer (or PayPal for international customers). I will also allocate a slot for you in the batch production schedule.
Please be aware that you have 48 hours to pay the deposit to secure your slot in the batch production schedule. Batches are scheduled on a ‘first come first serve’ basis from payment of the invoice and a delay in payment may result in a longer lead time due to the reallocation of your slot.
-
All orders will be shipped fully insured and with a tracking service. The cost of shipping is dependent upon the size of your order. A shipping and handling fee will be included in any invoices and on quotes where a shipping location has been provided.
UK orders - 1-3 days
International orders 1-3 weeks (depending on location)
Letterpress price guide
Much of the cost of letterpress is down to the set up of the print run. A number of other factors also inform the cost, including the number of colours, the size of print area and the level of design service required. Therefore, the following prices are intended as an approximate guide only.
Prices are for single-sided, single-colour print and do not include the cost of paper. Price is per individual print.
There is no minimum order requirement for printing but you may want to consider the minimum order requirements of a made-to-order batch of handmade paper (e.g. the minimum order for a batch of A6 handmade paper is 50 sheets even if you are only printing on 25). Please see 'Made-to-order Handmade Paper Service' for info on paper costs and minimum order quantities.
The ‘SIZE’ column in the table below refers to the print area size and not the paper size.
Thank you for taking the time to read this information. I hope it is a helpful resource for you as you plan your projects. I look forward to printing your beautiful designs!
Lauren x